The Resurrection of 550 Arlington Avenue: Phase 1
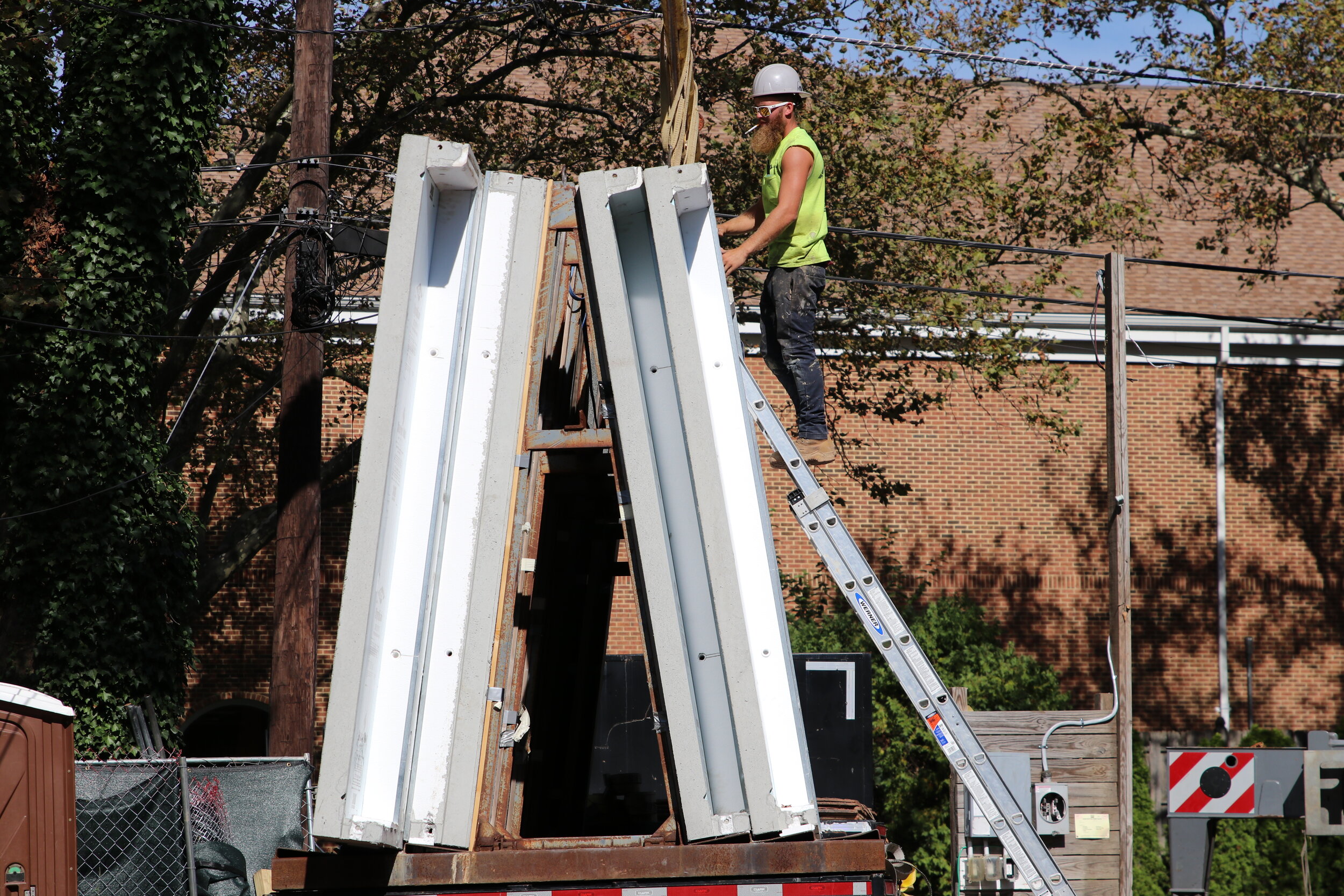
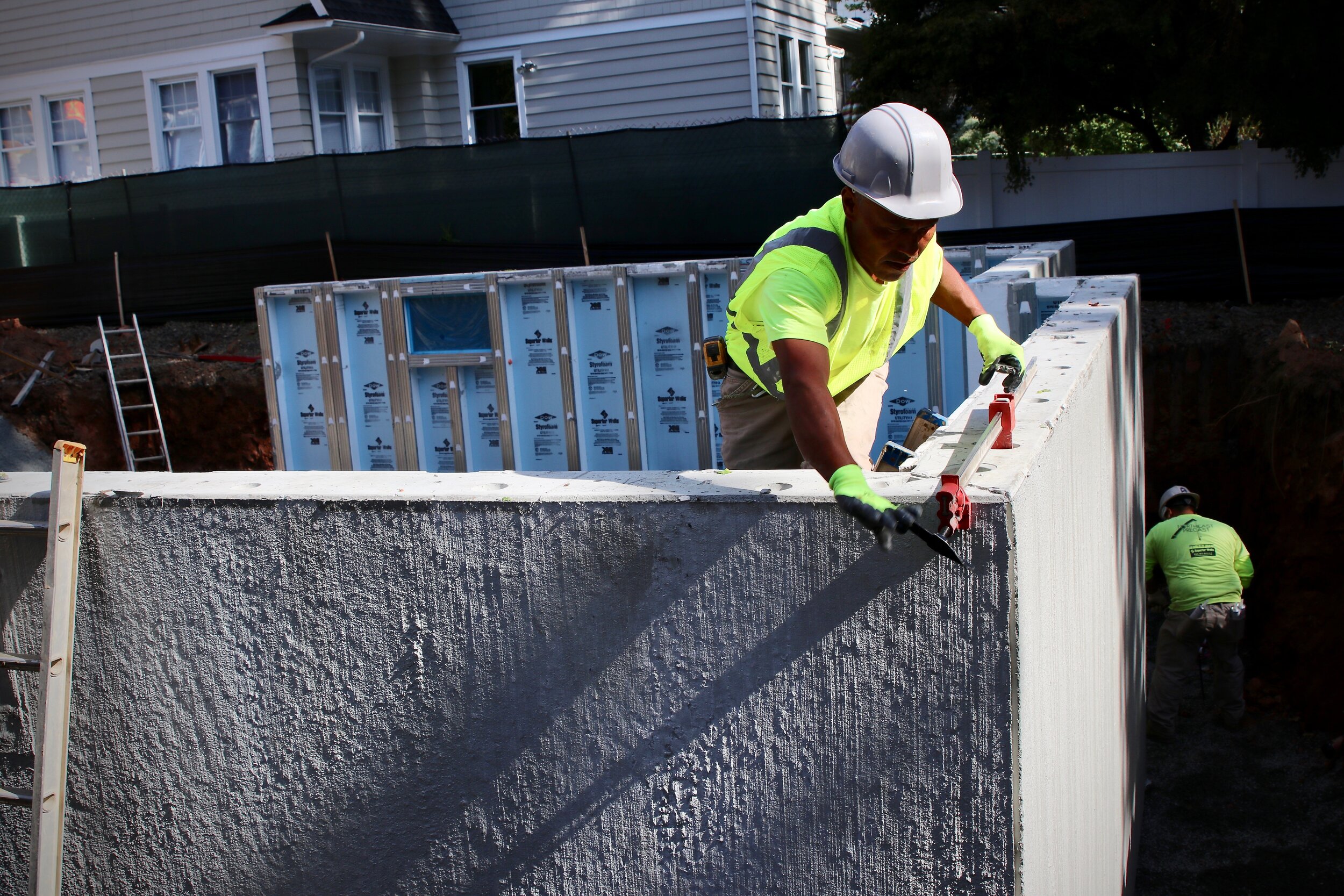
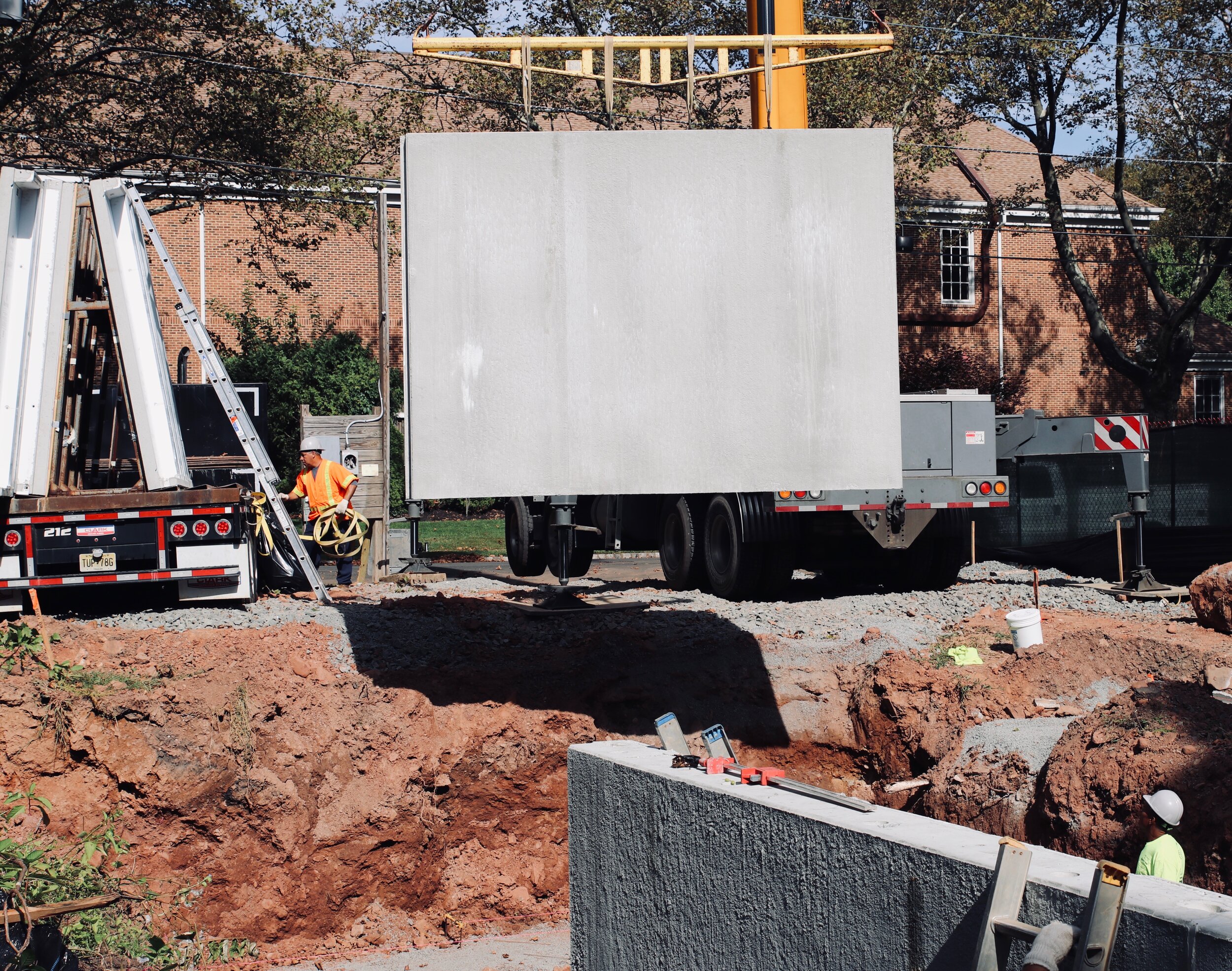
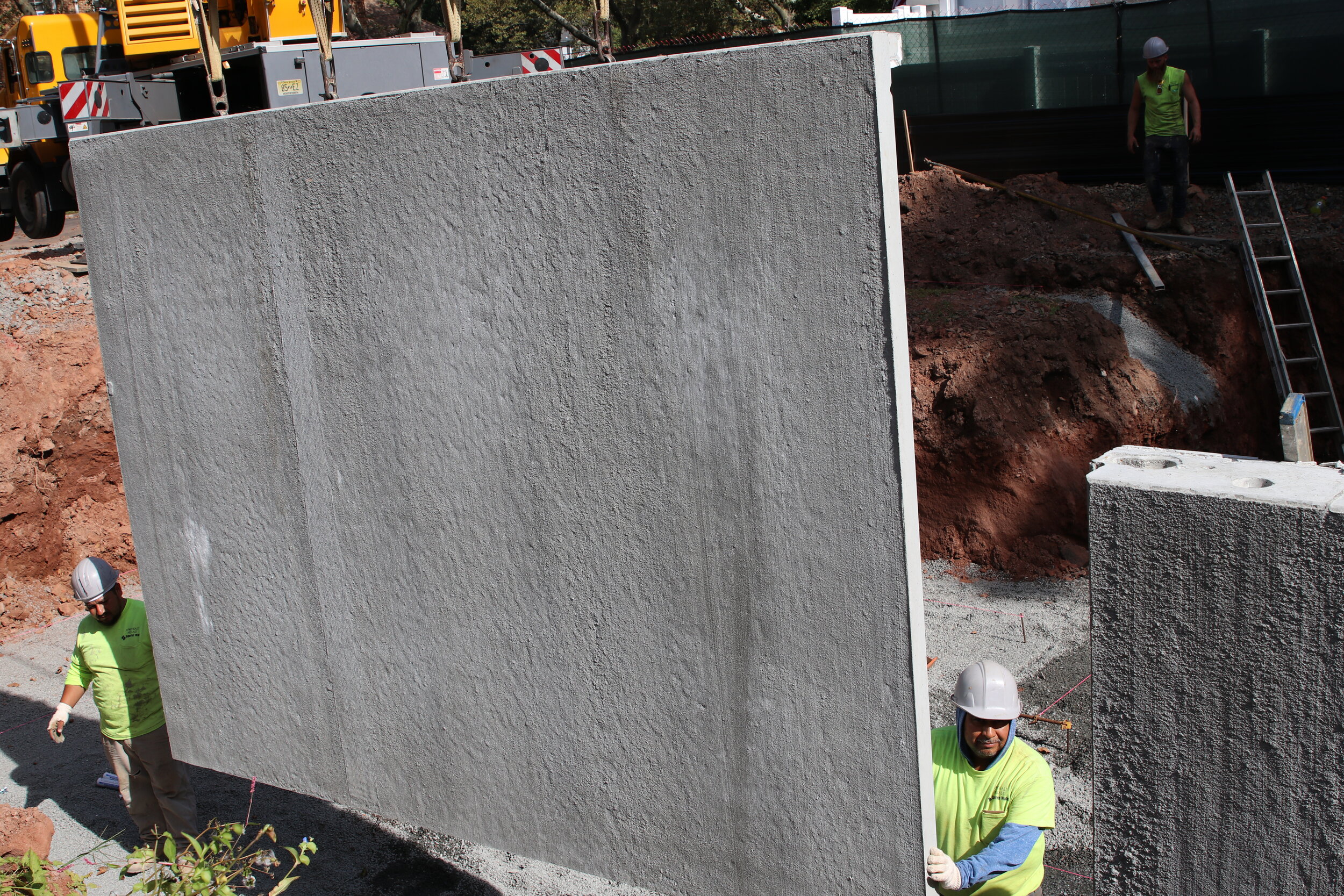
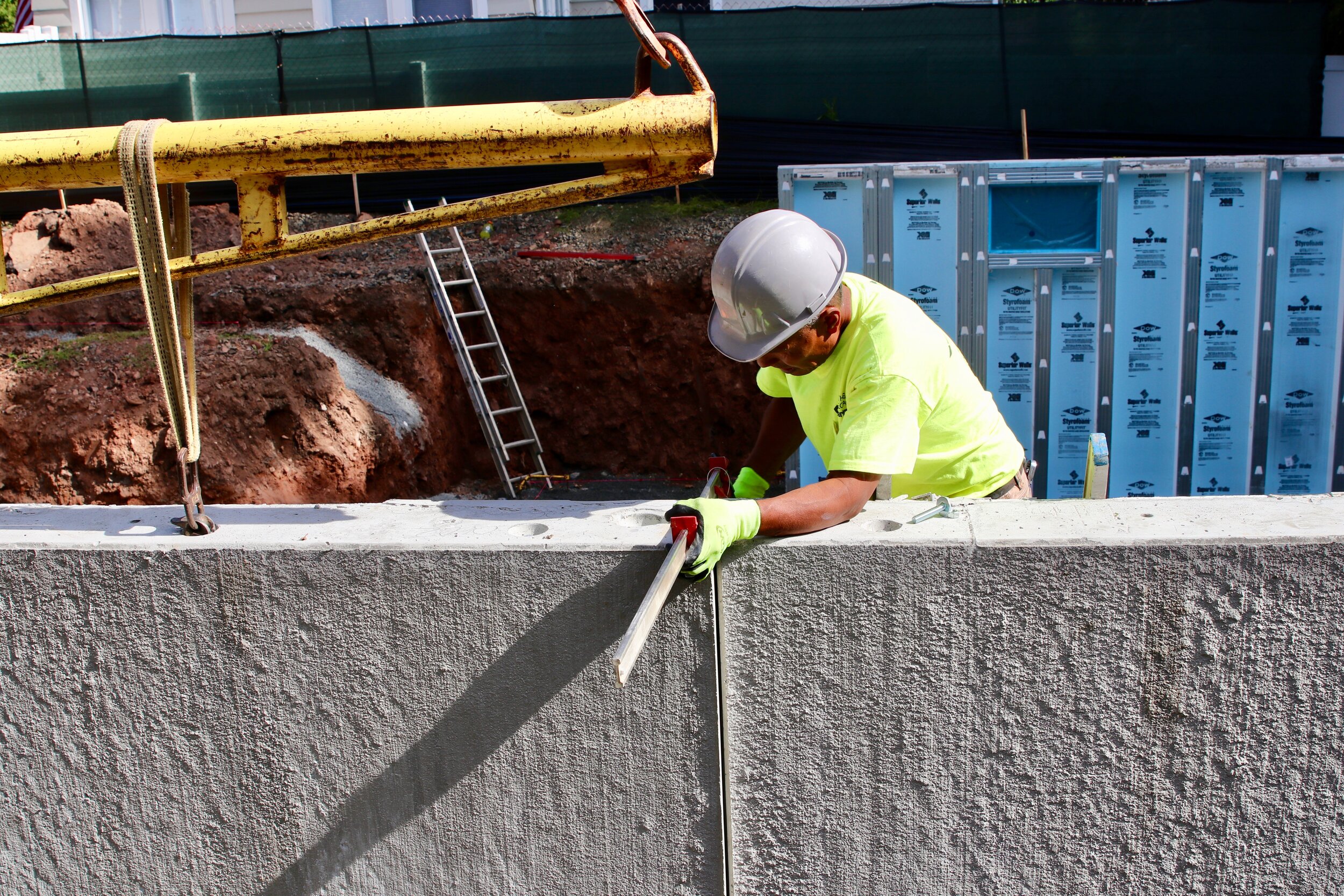
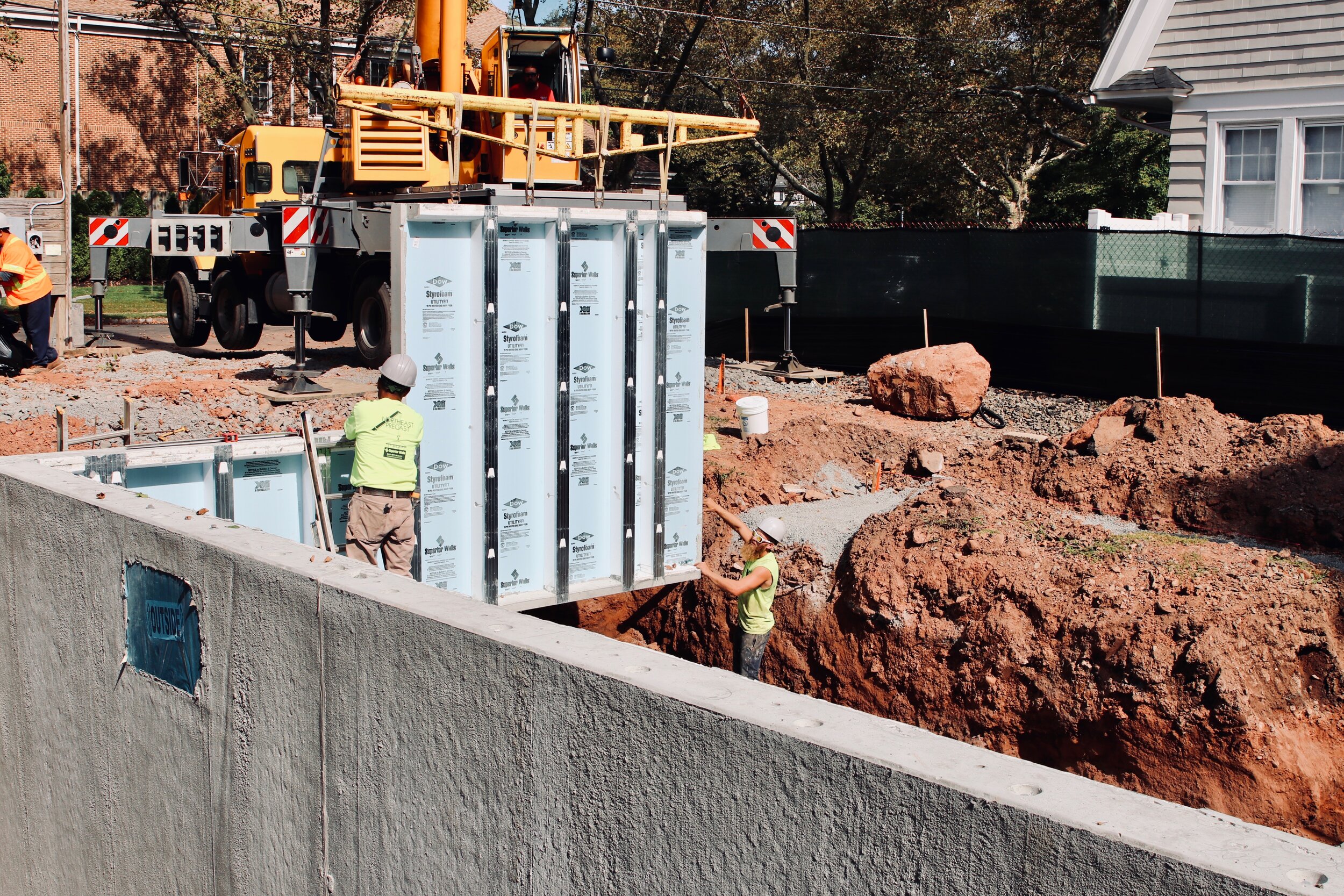
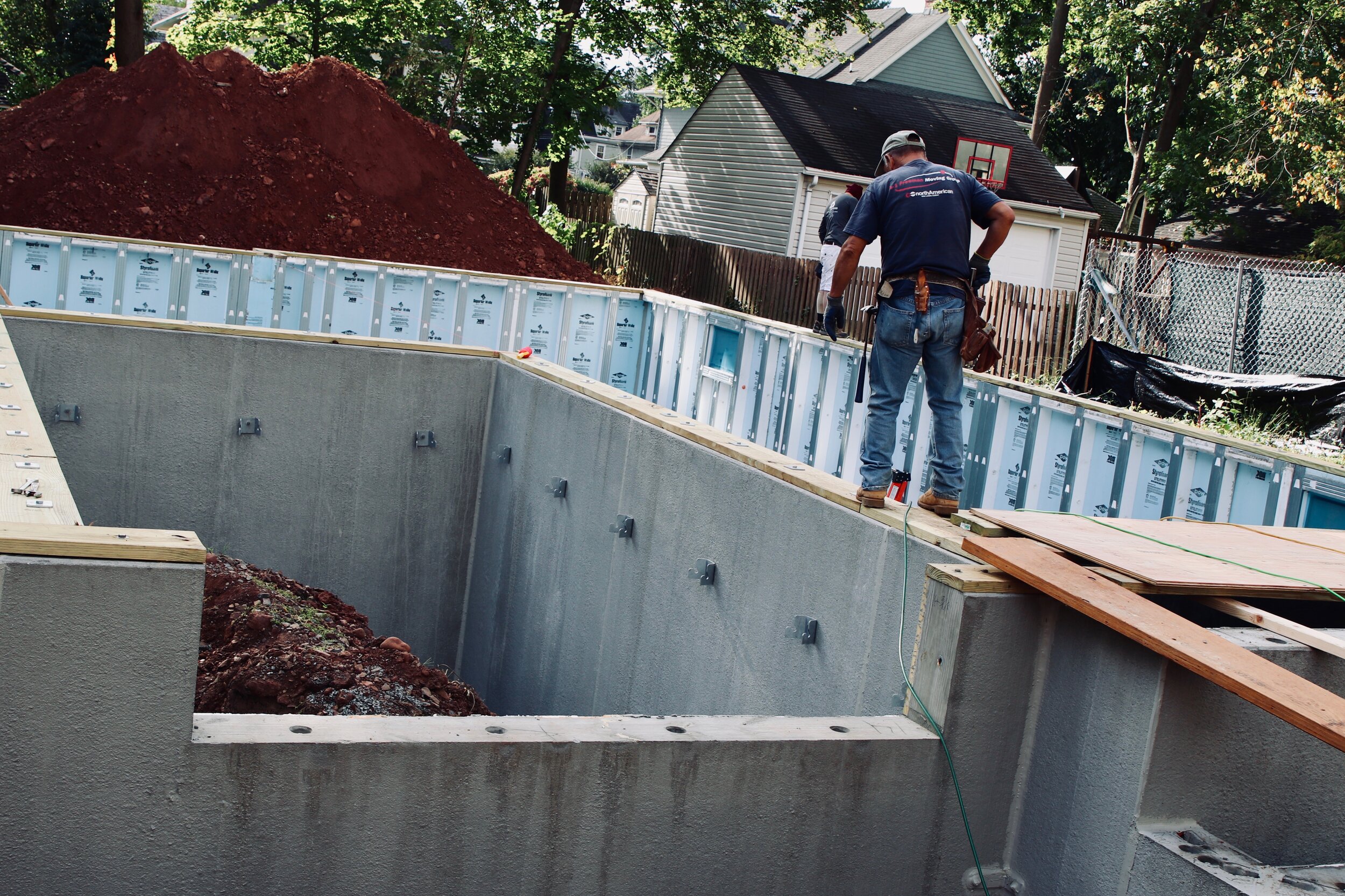
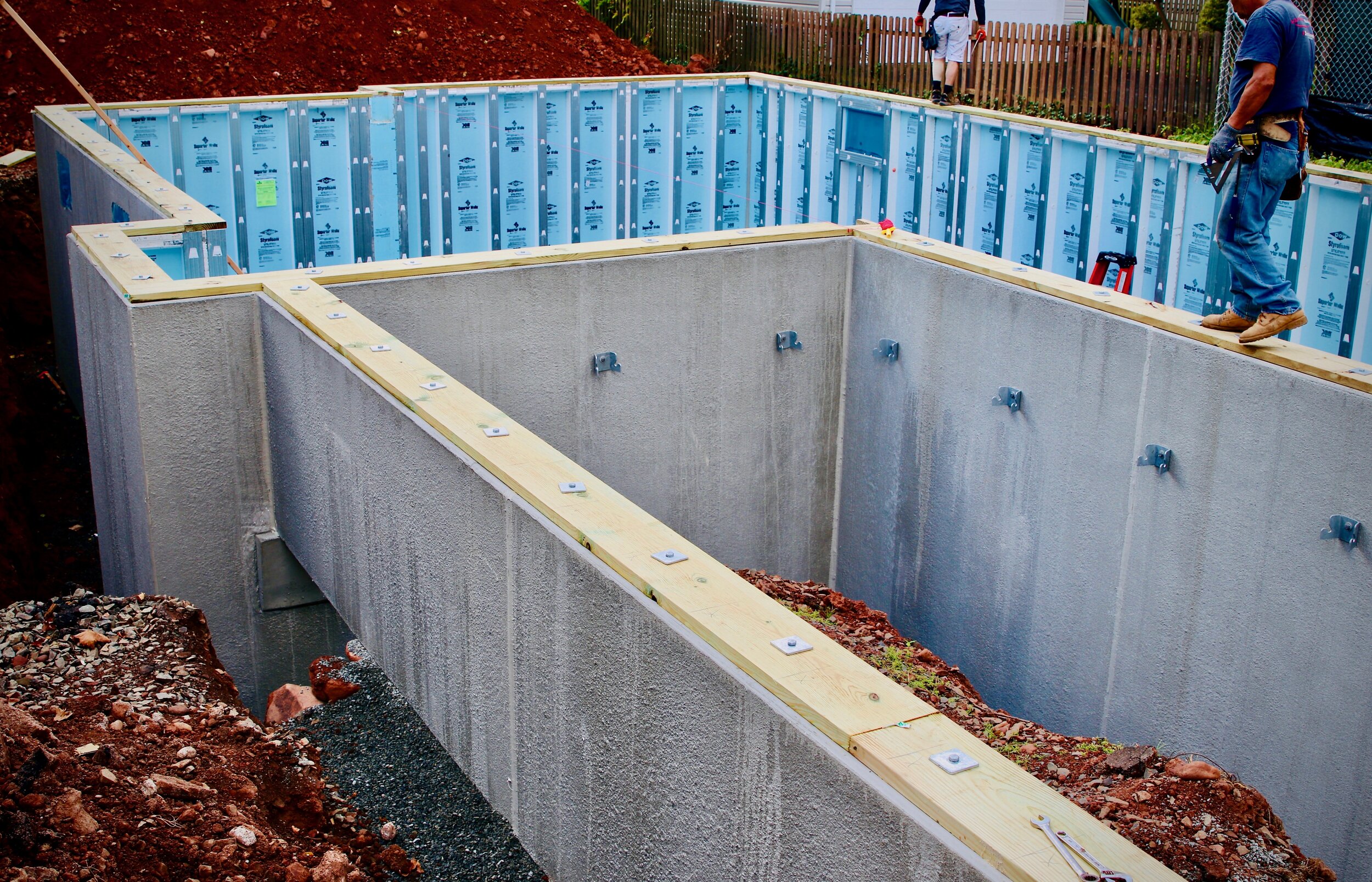
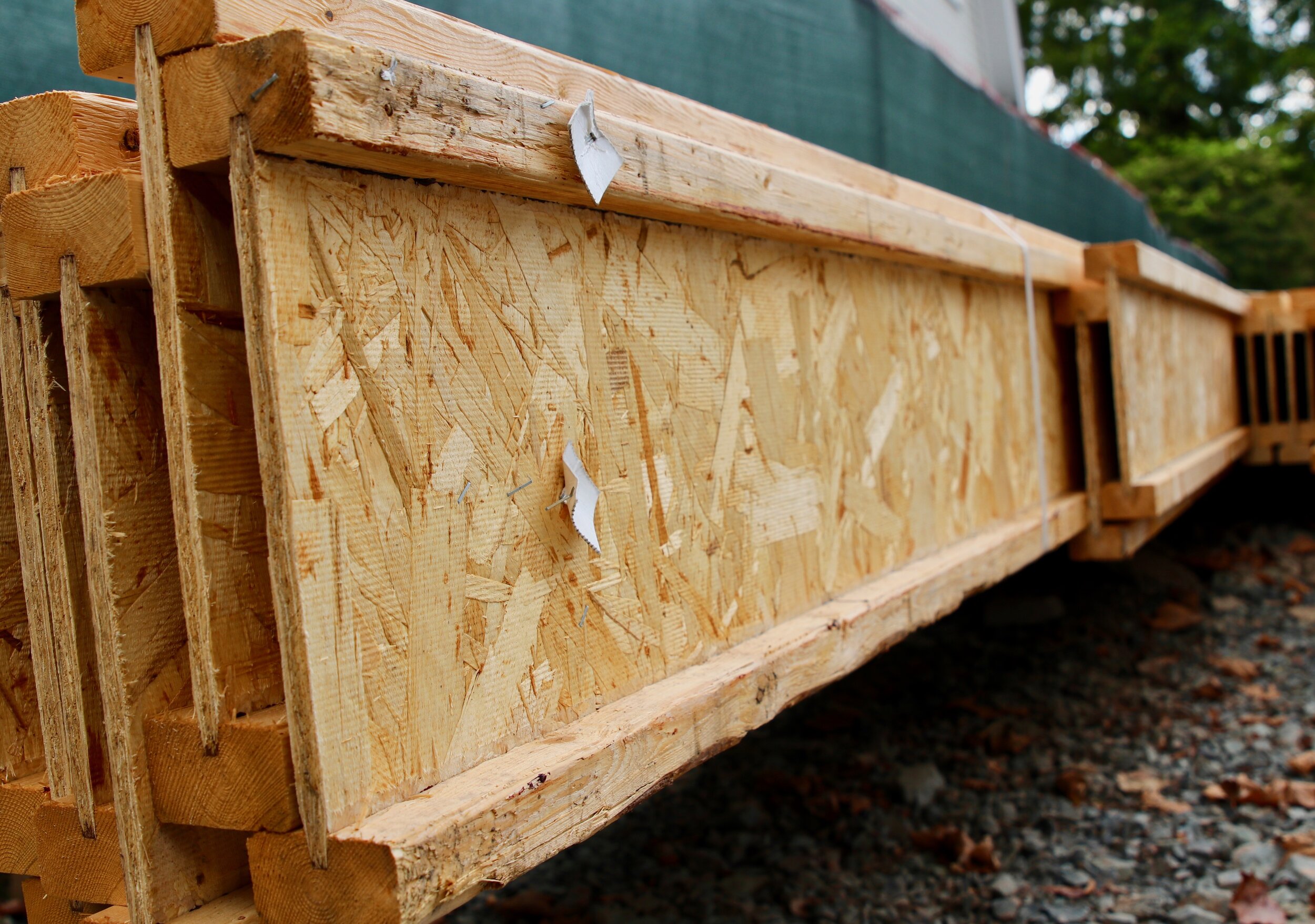
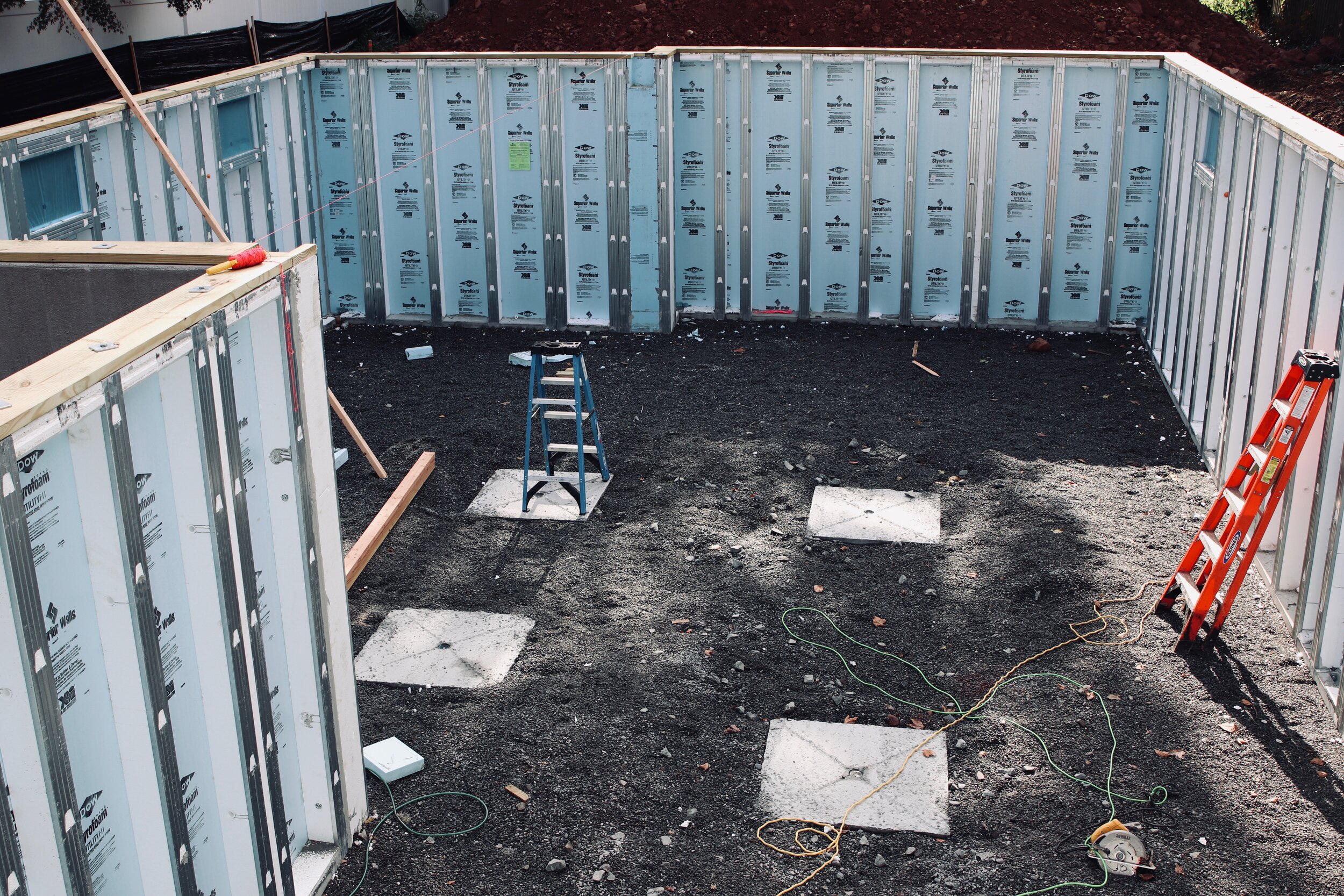
“Change is the law of life. And those who look only to the past or present are certain to miss the future.”
Custom Home Builders
Knocking down an old home and starting fresh may seem a little crazy to some, but in 100+ year old towns near large US cities like New York, Chicago or Los Angeles, it’s becoming the norm.
Long established towns near transportation, or with freeway access to metropolitan cities have long lost access to affordable land, for sprawling subdivision.
As a result custom home building businesses have sprung up providing individuals with the opportunity to buy, not just an older renovated home in a desirable location, but a newly built house from the ground up with curated finishes.
This is where investors and skilled custom home builders step in.
First, investors assess the value of the land.
Next, these investors also tally the cost to knock down the old home, materials for the new home, labor costs, carrying costs, and additional money needed to effectively market and sell the home for the a reasonable profit.
In many cases the sum of the parts doesn’t produce a big enough payoff to make the job worthwhile.
In other scenarios, and in a hot real estate market, the custom home builder can make tens if not hundreds of thousands of dollars by starting from scratch.
Custom home builders also need to be aware of the aesthetic of the neighborhoods in which they are building.
It’s important to capture and maintain the design aesthetic of the surrounding homes by creating a new home that seamlessly fits the neighborhood’s era.
If the new home’s design is significantly out of place, it could hurt the value of the surrounding properties making for some unhappy neighbors.
In the case of 550 Arlington (note the artistic rendering of the home above), Anthony Louis Custom Home Builders was careful to make sure that the integrity of the home’s architectural design matched the turn of the century style, and neighborhood aesthetic.
Before: 550 Arlington Avenue
Built In 1922 | 3 Bedroom | 2 Bathroom
Photo: MLS
After: 550 Arlington Avenue
Custom Built In 2020 | 5 Bedroom | 6 Bathrooms
Photo: Rendering Courtesy Of Anthony Louis Custom Home Builders, LLC
After
The New Home: 550 Arlington Westfield, NJ
Size: 5 Bedrooms / 5 1/2 Bathrooms
Style: Exterior Colonial Center Hall Design
Location: Nestled directly across the street from the town library
Completion Date: Spring 2020
Before
The Original Home: 550 Arlington Westfield, NJ
Size: 3 Bedroom / 2 Bathroom
Style: Traditional Colonial Exterior
Knock Down Date: June 2019
Westfield, NJ
Westfield, NJ is an idyllic town that marries the quaint history of NJ with the bustle of a New York City commuting lifestyle.
Situated just 24 miles outside of Manhattan on the Raritan Valley NJ Transit train line, and with bus service to New York City, Westfield has the reputation of offering a tightly knit community feel while offering top notch restaurants, shopping and highly ranked schools.
These qualities lend themselves to valuing a new custom home build on a .17 acre lot at $1.275 million.
So, just how do you go from a small 3 bedroom 1922 knock down to a 3100 square foot 5 bedroom / 5 1/2 bathroom gem?
Change. And custom home builders.
Demolition And Digging
Now that the home has been purchased, demolished and the land is cleared, it’s finally time to start the process of digging the hole for the new home’s foundation.
Photo: Anthony Louis Custom Home Builders - 550 Arlington Avenue
The surveyor / engineer plans and the architect’s foundation plan are used to very carefully map the outline of the home and begin the digging.
Typically, when a basement is part of the plans, a hole 6 feet deep is dug.
As the digging begins, the builder must be extremely careful to monitor the dig for any existing ground water.
Hitting ground water is never the preference,\ since it requires additional steps (and added cost) before the foundation can be laid, whether it's a conventional cement block, form concrete pour or in this case, a Northeast Precast Foundation.
If The Builder Hits Ground Water
If ground water appears, the builder will continue to dig deeper in effort to measure and manage the water’s presence.
To mitigate the presence of any ground water, the builder must bring in additional fill to raise the grade.
A layer 4”-5” layer of track stone at the base of the hole
Track stone is 2 ½ - 3 inches in width
Track stone does an excellent job of creating some additional footing for the home
Photo: Track Stone Example
Next 4”-5” layer of 3/8 pea stone gravel is situated on top of the track stone
The total additional stone layer is now between 8-10 inches in depth, providing a home with added stability and freedom from run-off water.
BWAB: Hole for new home with track stone and pea stone
Foundation Mapping
Once the stone layers have been set, and there has been extensive testing for ground water depth, the engineer is called back for very precise mapping of the foundation.
Here we set three pins in the foundation - two in the back corners and one in the front corner of the lot. These established points are called foundation location, and are now the reference points for the foundation crew to set the foundation.
Laying The Foundation Walls
On the day that the foundation wall is delivered, the precast subcontractor begins by setting the lines for the walls and the elevation from the hub by 1/8 of an inch or less.
The precast team lays pink string lines where the walls are to be dropped.
Holes are dug in the pea stone and flag stone for the concrete footing pads that will eventually support the lally columns that will hold up the home’s first floor.
Photo: Build With A Bang - Lally Column Markers
Benefits Of A Precast Foundation
The precast installation process typically takes just 1 day. With a precast foundation or a concrete wall panel, there is only a need to dig an additional 8 inches since and there is no need to pour concrete footings. This is a significant time, labor and cost savings to the builder.
Precast Materials
Precast foundation walls are made of approximately 3 1/2 - 4 inches of concrete, a layer of insulation, waterproofing and studs - are all prefabricated in a factory and hauled to the site. Prefabricated foundations save on cost and get the job done faster.
Additionally, studding is already embedded in the precast and makes drywalling the basement that much quicker.
Photo: Build With A Bang Precast Foundation Installation
The precast company delivers a crane to the site, lifts the panels from the truck and drops them precisely to the pink string.
Once the panels are set exactly to the line, the worker applies a liberal amount of epoxy to the joints, and then bolts them together at the top and bottom of the wall.
Once the foundation is set, you can start framing the next day.
Photo: Precast Foundation Wall Lifted In To Place
Each of the studs are metal, and in this case 16 inches apart, on center.
In a precast foundation you also have sleeves for piping for the plumbing, and wiring for the electrical.
If you don’t have the necessary mechanicals, you can still drill through the precast to include whatever mechanicals are necessary.
And unlike a traditional foundation, with a precast foundation you don’t need a foundation inspection.
A Traditional Foundation Wall Pour Vs Precast
Photo: Example of a Standard Concrete Footer Pour
Since the Arlington house was built with a precast foundation, we thought it might be interesting to compare a factory developed foundation vs. a more traditional foundation.
In a traditional foundation pour (remember Arlington is precast), after reaching undisturbed/virgin soil and mitigating any water issues, you must reach a point in the ground that is below the frost line so any concrete poured doesn’t buckle and cause damage to the structure.
Next up, constructing the forms for each of the footings, and then pouring the concrete in to each of the forms.
Like the precast walls, the concrete acts as the “feet” for the home, spreading out the weight, and providing the stability needed to build and maintain the structure.
After each of the forms set there is another inspection.
Once the concrete cures, you break off the forms from the concrete.
Now, it’s time to set the forms on top of the footings for the wall pour.
This process can take up to 2 weeks.
A longer process, but an argument for either a traditional wall pour or precast foundation can certainly be made.